Create an optimal working environment. With our Technical Facility Management, we take care of operation, maintenance, inspection and repair of your building services or develop tailor-made concepts for modernization. Also, we rectify faults in the shortest possible time and ensure the supply of your production buildings from hot and cold water to compressed air and electricity.
Technical Facility Management
For smooth production processes: Technical Facility Management from Leadec
Technical Facility Management is one of the core measures to ensure the functionality of a company. This is exactly where we start. We support you in building services operation, maintenance and inspection and in the development of customized maintenance concepts.
Our employees are our strength. Their know-how and experience in the field of technical facility management ensure smooth maintenance and repair processes. In addition, all work is carried out during the production process – without disruption. And so that you can trace everything, our employees document all work in our CAFM system for complete transparency.
No matter which area of Technical Facility Management is concerned: We are at your side. So that your production processes run smoothly and you can concentrate on your core business.
Our services in Technical Facility Management
Facilities maintenance
- Maintenance with a high percentage of own work of over 70%
- Inspections according to laws and standards
- Provision of emergency and fault-clearing services: 24/7 on-call service with own call center
- Digital asset data collection, evaluation and documentation review
- Establishment of a CAFM system, if necessary, multilingual
- Vibration measurement on rotating parts, leak detection on compressed air lines, thermography, roof inspection by drone/thermal imaging
- Technical maintenance measures for building services (DIN 276 cost groups): execution of maintenance measures (maintenance, repair, operation, expert inspections, support of expert inspections) by our Leadec experts
Building automation
- Detailed basic analysis for building services
- Integration of individual automation solutions
- Installation and commissioning of building services systems in factories and offices
- Support and maintenance of plants and equipment during operation
Energy management
- Energy supply of machines and technical equipment
- Ceiling lighting optimization
- Operation of the power house, utility supply systems, gas and compressed air supply
- Energetic optimization measures
- Energy audits/filter audits
Projects and modifications
- Machine relocations
- Machine dis- and reassembly
- Adaptation of the technology to the latest state of the art
- Extensive documentation of the projects
- Modification during operation
- Guaranteed machine relocation
Technical facilities management
Air condition / Ventilation
- Ventilation, refrigeration and air conditioning technology
- Refrigeration plants
- Process cooling water systems
- Single and multi-split systems
- Cooling ceilings
Heat
- Heating systems
- Supply networks
- Central heating systems
Warranty management
- Use of a CAFM documentation management system
- Calendar and deadline management
- Defect recording and checking of documentation
- Implementation of initial inspections/tests
Janitorial services
- Stocktaking
- All services to ensure the building functions such as:
- Safety inspections
- Safety lighting systems
- Elevator attendant services
- Ensure the cleanliness of the property
- Compliance with the house rules
- Minor repairs
- Control of escape and rescue routes
- Functional testing and repair of windows, doors and gates
Water and waste water treatment
- Plumbing
- Sanitary facilities
- Water treatment
- Drinking water supply
- Drainage
- Fire water systems
Your advantages
- Concentration on the core business
- Highest plant availability and fast response times
- Efficient building management
- Value retention of the building and the building services
- Careful planning to reduce costs (cost savings through outsourcing to service providers)
- Energy savings through systems and operational optimizations
- Fast troubleshooting
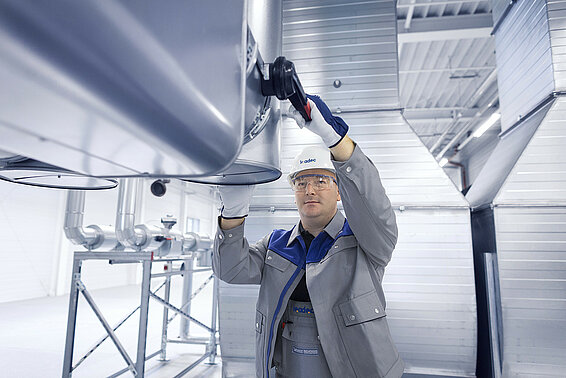
Digital solutions for Technical Facility Management
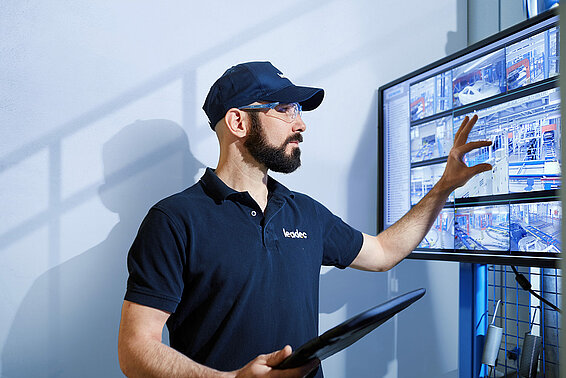
With our digital offer we provide transparency and increased service quality. Suitable for every service. These solutions optimally complement production maintenance.
Smart Condition Monitoring
With Smart Condition Monitoring, we not only provide preventive maintenance, but also intelligent condition monitoring. In three phases, we detect anomalies, install sensors or IT systems and finally define intelligent guidelines for action.
Digital Equipment Capture
Our Digital Equipment Capture records systematically asset master data and creates a high level of transparency - throughout the entire process. By implementing the data in a CAFM system, maintenance can be better planned.
Contact
Want to learn more? Ask us.
Please send us a message: info-brazil(at)leadec-services.com or use the contact form.